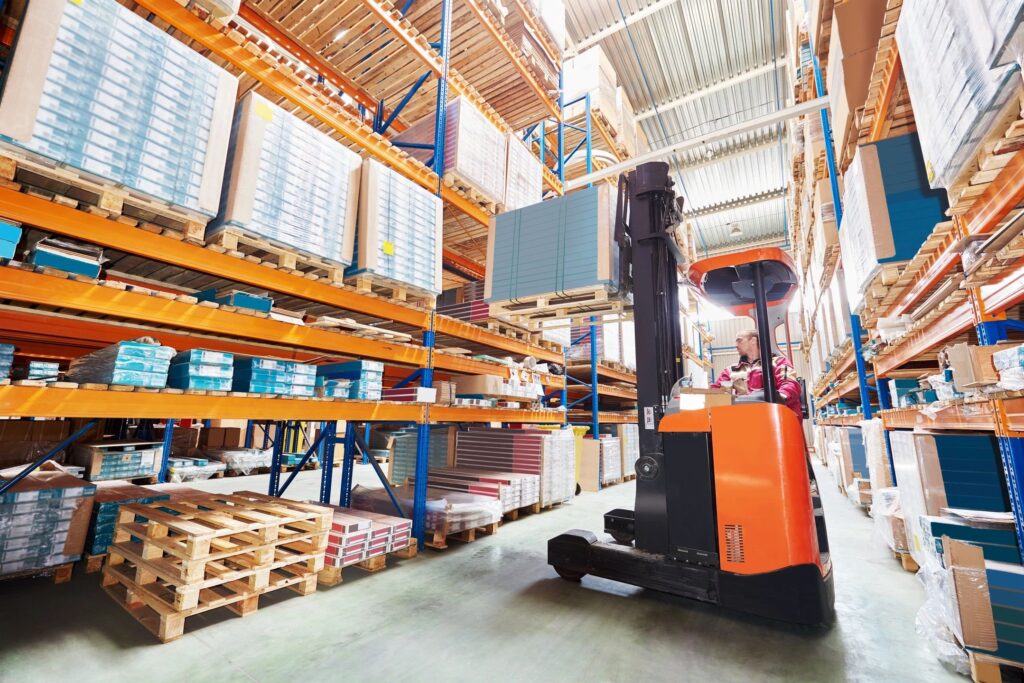
The Third-party logistics (or 3PL) refers to the outsourcing of ecommerce logistics process to a 3rd party business, including inventory management, warehousing, and fulfillment. 3PL providers allow ecommerce merchants to accomplish more, with the tools and infrastructure to automate retail order fulfillment. We don’t know who coined the term “third-party logistics,” but companies began trending toward outsourcing inbound and outbound logistics services to 3rd parties within the 1970s and ‘80s.
With the growth of ecommerce within the ‘90s and 2000s, the term 3PL has become ubiquitous, and 3PLs have expanded their services. The availability chain integration of warehousing operations and transportation services has become what we now call third-party logistics.
The 3PL order fulfillment process
If you’re considering working with a 3PL company or are unaccustomed outsourcing shipping, what goes on in a very 3PL fulfillment center could appear sort of a recorder. But the 3PL fulfillment process doesn’t must be a mystery, nor should it be! So what exactly happens at a 3PL’s ecommerce warehouse once a customer clicks “Submit order” on your online store? Let’s explore the whole process from start to complete.
Receiving
A 3PL can’t ship orders without inventory there. The “receiving” of inventory in an exceedingly 3PL warehouse refers to the acceptance of incoming inventory followed by its storage. Each 3PL has its own processes and capacity for receiving and storing inventory. Requiring clients to fill out a Warehouse Receiving Order (WRO) so we all know which products we’ll be receiving and the way many units helps us stay organized and timely with receiving. Meaning, we will start fulfilling your orders more quickly and efficiently.
3PL Warehousing
Once we receive your inventory, we store your items in our fulfillment centers. Each contains a separate dedicated storage location, either on a shelf, in a bin, or on a pallet. Different 3PLs have different storage capacities; not all 3PL warehouse space is made equal. It’s important to figure with a 3PL that has quite enough space for storing for your current inventory — as your product and order volume grow, your 3PL storage must be ready to scale with you.
Picking
When a customer places an order, it’s time for the 3PL fulfillment process to start. (You may have heard the phrase “pick-and-pack fulfillment” before) Some 3PLs require you to manually upload orders to their system. Sometimes, this involves spreadsheets including order details, customers’ shipping details, and more.
Other 3PLs have sophisticated technology that integrates directly along with your ecommerce platform or marketplace. These 3PL fulfillment software integrations bring orders, shipments, inventory tracking and stock levels, and more together in one place to streamline the fulfillment process for more automated shipping. This includes automatically pushing customers’ online orders to your 3PL as soon as they’re placed. When an order is distributed to your 3PL, it’s assigned to the warehouse picking team. The picker receives a picking list of the things, quantities, and storage locations at the ability to gather the ordered products from their respective locations.
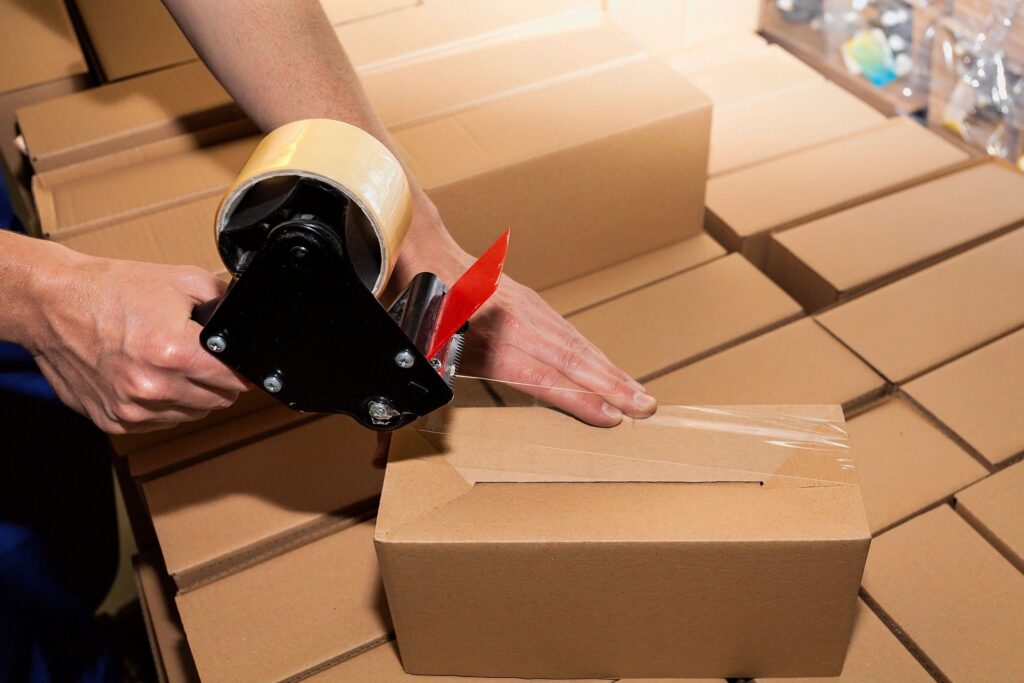
Packing
When all items in an order are picked, it’s time to urge them securely packed for shipping. The packing materials used will rely on your 3PL’s capabilities, your brand preferences, and also the items being shipped.
The most common standard packing materials include:
Unbranded boxes, Bubble mailers, Poly bags, Packing tape, Paper-based dunnage
Some 3PLs will charge for packing materials as a separate item, while others include them as a part of their fulfillment management services. As experienced shippers, the 3PL will choose the simplest packing materials to both protect your products and achieve very cheap practical dimensional weight. They’re going to also optimize packages, so you don’t need to split shipments. Using the correct packing materials can help keep logistics costs low.
Shipping
The next step is shipping your order. Most 3PLs will purchase and print shipping labels on your behalf. Some 3PLs have preferred carrier partners, while others compare shipping costs from a range of carriers. The latter helps 3PLs offer clients the foremost affordable pricing possible for the delivery speed that every customer decides. The carrier and shipping speed for every order depend upon the 3PL’s partnerships and policies also because the ship options offered by the client and selected by the tip customer. Once the order ships, 3PLs with the integrated technology mentioned above will automatically push tracking details to merchants’ online stores.
If you are looking for 3PL services visit our webiste at weboxprepcenter.co